As part of AME 40423 – Mechanisms and Machines, design problem asked students to perform a dynamic simulation of the motion of a four bar mechanism powered by a 12V motor-gearbox combination lifting a large steel block.
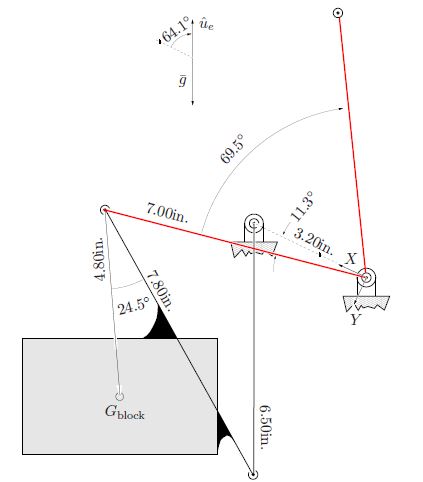
The design requirements in order of important were as follows:
- Block must move to a specified intermediate position from startup within 0.5 seconds
- The machine must reach steady-state operation within 2 seconds of startup
- The machine must have an input speed coefficient of fluctuation less than 10%
- Cost should be no more than $60
- Drive system should weigh no more than 2 lbf
For the sake of calculation, the mechanism was approximated as a 2 dimensional, planar mechanism, and the links were considered to be massless, as the mass of the steel block was significantly greater. First, the behavior of the mechanism as a function of input angle was considered using the position equation and first and second order kinematic coefficients. Next the kinematic coefficients of the points of interest of the mechanism were calculated and used to find the motor torque required for static equilibrium at all positions of the mechanism’s input. An initial motor-gearbox combination was selected, and used to ensure proper implementation of dynamic simulation giving machine position and velocity for a given driving motor.
Finally, with a dynamic simulation code created, the performance of the initial motor-gearbox selection was evaluated to determine whether or not it met the design requirements. The initial motor-gearbox selection only met the second and fifth design requirements, thus a new motor-gearbox selection was sought such that the system would be more optimized to meet design requirements. A selection was eventually chosen such that design requirements 1, 2, 3, and 5 were all met. It was also determined that given the product prices of the vendor from which the motor-gearbox selection was required to come from, the fourth design requirement was unrealistic.
The final report and summary of the case study as well as the development and use of the dynamic simulation can be found by following the link below.
James Cole AME 40423 Design Set 2 Dynamic Simulation Case Study