I am currently the Safety Officer of the Notre Dame Rocketry Team for the NASA University Student Launch Initiative 2018-2019 competition. As an officer of the team, I gained a great deal more responsibility, especially since NASA has an intense focus on safety and documentation. Previously, the team had struggled with its safety implementation and documentation, which caused the team’s scores in those areas to suffer. This was due to the complexity of building a safety policy from the ground up, as the guidelines from NASA were not as explicit as their technical guidelines and design requirements, and because safety covers all aspects of the team’s extremely multidisciplinary functions and squads. Each squad has a different and extremely complex technical challenge, which is why the team is organized the way it is. In order to create proper safety policy and documentation one must have a technical understanding of the function and activities of each squad, as well as a technical understanding of the system/payload they are in charge of. I took on the job knowing this, as I felt I could make a significant and lasting impact on the team.
I first started by defining the problem, and then derived the requirements that followed from this problem. I decided that the culture of the team about safety would need to change to be a positive and involved one. To do this I first decided that standards and guidelines for team operations should be created and compiled into a handbook; the handbook would guide the operations of the team, with safety as an implicit part of every operation, rather than being shoe-horned in. I also set about making safety a more regular part of the team by making the safety officer a more integral part of the team itself. To do this, I have been kept myself informed and up to date on all aspects of the designs and operations of each technical squad, and have maintained open lines of communication with the leads of each squad. This has meant that I have had to have technical knowledge of every aspect of the project to at least a basic level if not more involved. I also created a multidisciplinary committee of members from all the technical squads of the team, in order to assist me with accomplishing all of these tasks and provide further expertise on the designs and operations of each squad.
The results have been phenomenal, the team has published a safety handbook and document that compiles the SDS (Safety Data Sheet) documents of every material the team interacts with. These documents are publicly available here:
The team has also standardized the use of PPE (personal protective equipment) for it operations, and has incorporated safety practices based off of publications by leading organizations such as OSHA.
I am particularly proud of my technical contributions this year. Thanks to my role as Safety Officer, I have been able to oversee the progress of all the technical design squads, and assist them as needed. I have been able to use my experience in fabrication and prototyping techniques to offer guidance on modifying part designs for feasibility of manufacturing and assembly; I have also been able to assist with fabrication of a wide variety of parts using CNC routers and mills, manual mills and lathes, CNC laser cutters, and other manual machines. This has not only allowed me to contribute to the team, but has also provided me with the opportunity to hone my skills and knowledge in these areas, as well as giving me opportunities to use my skills with CAD and CAM software. I have also been able to help guide designs by providing squads with suggestions for points of failure to analyse with numerical calculation or to design out completely.
Our rocket, Sorin I, is named for Fr. Edward Sorin – the founder of the University of Notre Dame. Sorin I has a carbon fiber and fiberglass airframe which is over 12 feet in length, with a fore diameter of 7.78 inches, an aft diameter of 6 inches, and a 3D-printed conical transition section between the two diameters to help reduce flow separation. The rocket carries two payloads, which are the air braking system and deployable unmanned aerial vehicle (UAV) payload. The air braking system is a variable drag system actuated by drag tabs that are driven by a servo connected to a crank-slider mechanism and controlled by an on-board microcontroller which controls drag based on barometer and accelerometer data to achieve a desired apogee. The deployable UAV payload essentially consists of two systems: the deployment system and the UAV system. The deployment system retains the UAV in fore payload bay during flight, then uses a planetary geartrain to correctly oriented the UAV so it is upright upon landing, and then deploys the UAV out of the rocket with a lead screw system. The UAV is is a quad-copter capable of both manual and autonomous control, which is tasked with taking off from the rocket, locating and landing on a an excursion area designated by a tarp within the competition area, and then deploying a beacon at the excursion area. The recovery system of Sorin I is a two-stage system that separates at apogee and deploys a drogue parachute and a bound main parachute using triple-redundant ejection charges, and then releases the main parachute at 500 feet above the ground using a double-redundant parachute-release altimeter. The systems on Sorin I are extremely complex engineering challenges individually, but combine to make an challenging and rewarding project that requires a highly organized and motivated multidisciplinary team of engineers to complete.
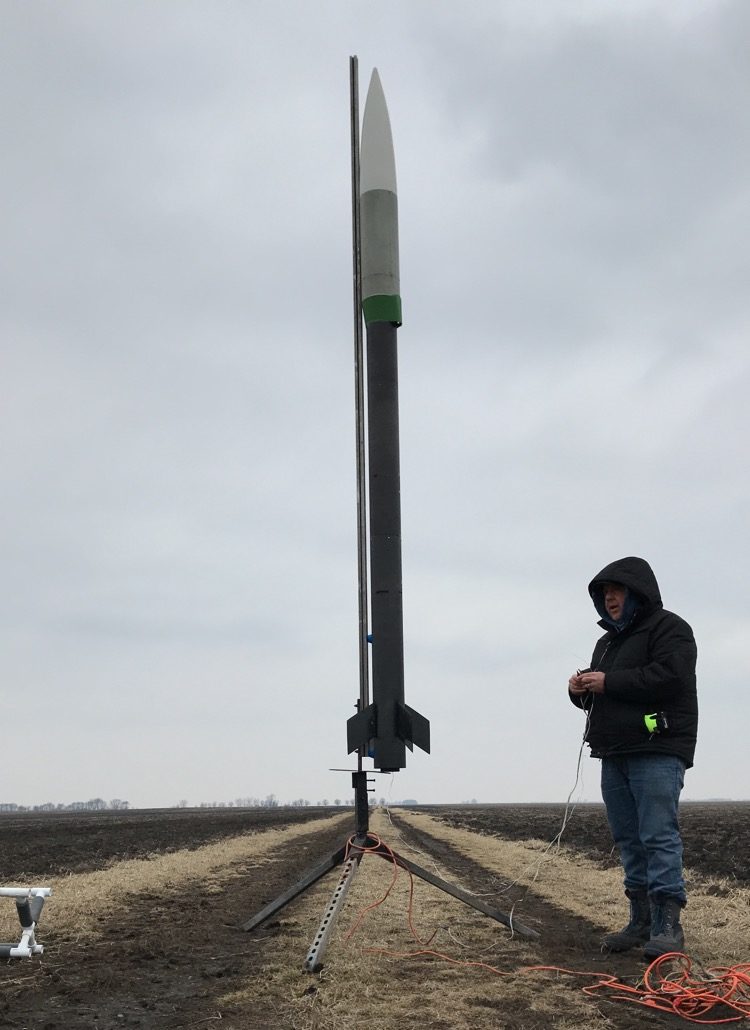
All in all, this year has allowed me to grow as a leader, by developing my project management and organization, while also allowing me to get exposure and opportunities for growth in a wide variety of technical skills and knowledge. The experience has made me a better engineer, and has also allowed me to see from a top level how engineering teams work best, and how I can be a valuable member of a multidisciplinary engineering team.