Location
Our lab is located in the White Field Research Facility at the University of Notre Dame. This space provides us with access to many scientific instruments and unique experimental tools.
Lab Instruments/Equipment
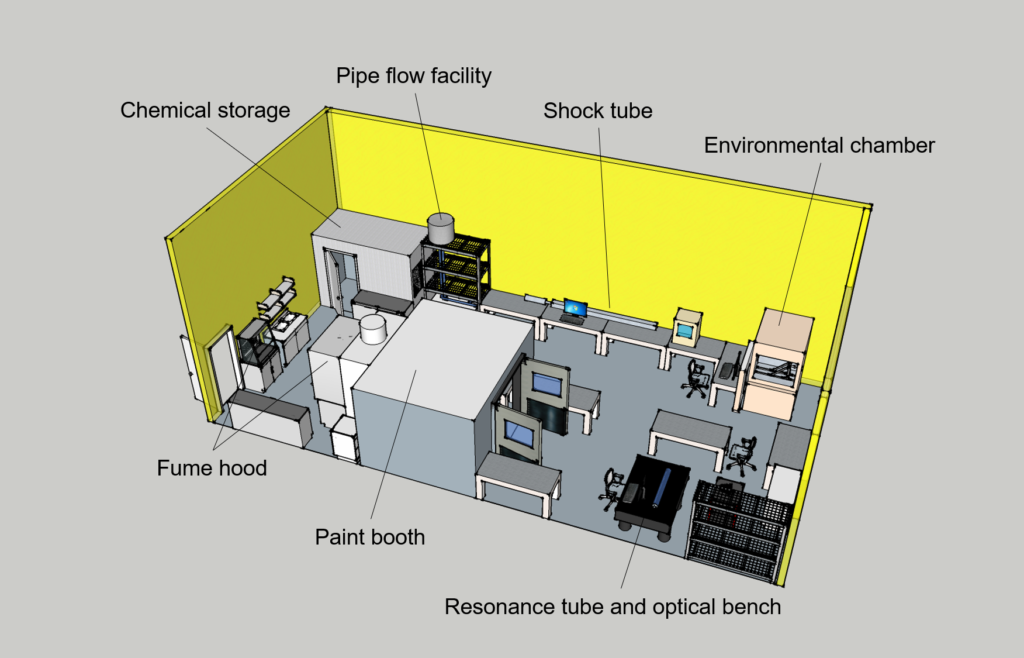
Within the Sakaue Lab, there are many specialized tools for the development and characterization of chemical sensors and coatings. These are described below.
Shock tube
The shock tube in the lab allows for the evaluation of the response of pressure- and temperature-sensitive paints (PSPs/TSPs) to a step change in pressure and temperature caused by a planar shock wave. The response time of the sensor is an important metric for unsteady measurements.
Resonance tube
The resonance tube in the lab allows for the evaluation of the response of PSPs to a high-frequency change in pressure caused by an acoustic source. The frequency response of the sensor is an important metric for unsteady measurements.
Pressure/temperature controlled chamber
The pressure/temperature controlled chamber is used to evaluate/calibrate the pressure- and temperature-sensitivity of developed coatings under various conditions. A controllable pressure and temperature range from vacuum to 500 kPa and -196 to 600 deg C. The severe condition, for example, cryogenic or high-pressure condition, also can be simulated.
Fluorescence spectroscopy system
The lab has a spectrofluorometer for various a fluorescence investigation such as light-emitting sensitivity, spectral sensitivity characteristic, emission intensity, wavelength dependency, etc. Spectroscopic characterization of developed luminescence sensors is conducted by the spectrometer.
Environmental chamber
The lab houses a reach-in environmental chamber to meet a specific environmental testing requirement. Currently it is mainly used for various icing testing. The chamber is capable of controlling humidity and temperature conditions. Large interiors (39.4″ x 35.5″ x 39.4″, 32 cu.ft.) enable us to construct desired experimental setup.
Contact angle meter
This unique meter allows us to precisely measure static contact angle and dynamic contact angle (sliding angle). The contact angle is an indicator for the wettability, which is dependent on the combination of solid substrate and liquid, as well as on the environment. It is useful for the evaluation of surface characteristic and degradatation (deterioration).
Large airfoils for icing test
As part of the ICE-WIPS project, our lab members designed a test article that incorporates three NACA 0012 airfoils with internal heating mats for icing research testing in NASA Glenn’s Icing Research Tunnel (IRT). This model has six areas that can be painted with different hydrophobic or anti-icing coatings to be tested against an uncoated baseline. We are always looking for partners to perform further icing research work using this model!
Pipe flow facility
The lab has a pipe flow facility which is used to characterize surface coating for pressure loss reduction. Bend pipe flow and straight pipe flow can be simulate.
Light sources
The lab has multiple light sources that can be used to excite the luminescent chemicals in the sensor coatings we develop. Powerful Lasers and LEDs with various wave length are available.
High-speed camera
To capture images for PSP and TSP measurements, high-speed cameras are required for unsteady applications. These cameras are also useful for flow visualization tests and the evaluation of icing phenomena. Both color and monochoromatic high speed camera is available.
Anodization system
In house anodization treatment is available to create a surface of a metal substrate with a microporous structure. This system is mainly used for developing a fast response type of luminescent sensors.
Fumehood
The lab is equipped with two fume hoods, one for chemical mixing and coating development, and another that is mainly used for the anodization process.
Paint booth
The painting booth with venitlator is installed for sensor/coating application. This booth accept large model to be sprayed.
Wind Tunnels
Various wind tunnels are available for use by our group members for experimental testing as part of the Flow Physics and Control group (FlowPAC) at Notre Dame. Several instruments for aerodynamic testing are also available, including a traverse rig, pressure measurement and flow visualization equipment, and assorted probes (pitot-probes, hot-wires, etc.). For details on FlowPAC and available facilities and instruments, see https://flowpac.nd.edu/.
(1) Flutter study with transonic wind tunnel (2) Boundary layer measurement over a flat plate with 2 ft by 2 ft subsonic wind tunnel (3) Cylinder flow visualization with 2 ft by 2 ft subsonic wind tunnel (4) Aerodyamic study using NACA 0015 airfoil with 2 ft by 2 ft subsonic wind tunnel (5) Aerodynamic study using NACA 0012 airfoil with 3 ft by 3 ft Mach 0.6 wind tunnel (6) Cavity flow noise measurment with transonic wind tunnel (7) Floating plate shear stress measurment with 3 ft by 3 ft Mach 0.6 wind tunnel