Supersonic facility SBR-50 – heated M=2 wind tunnel with a rectangular test section.
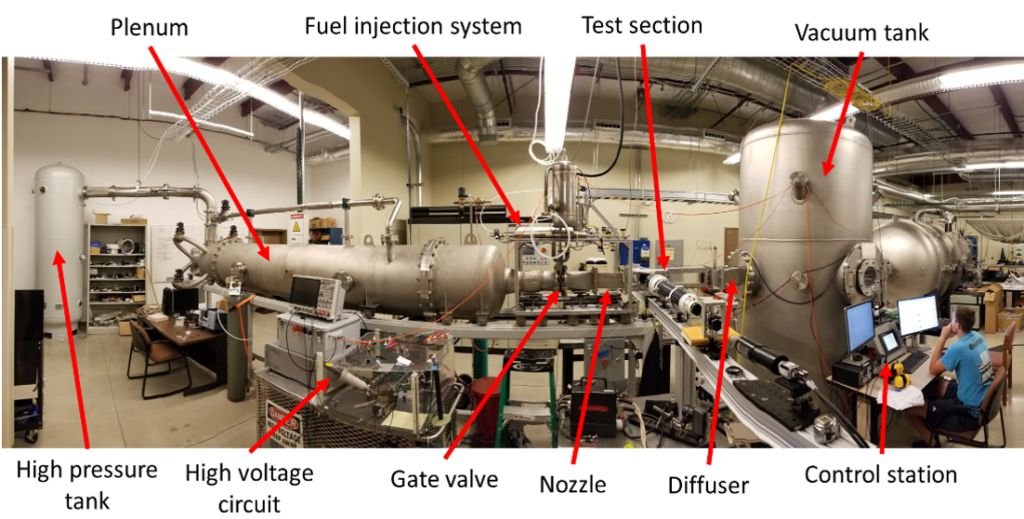

Top: The SBR-50 test facility photograph (October 2017). Bottom: Test section with optical windows installed.
Many experiments in the supersonic airflow are performed in the blow-down wind tunnel SBR-50. It was originally designed for a supersonic combustion and flow control research. The facility became partially operational in 2015 and fully operational in 2016. A photograph of the facility is shown above and the main flow parameters are listed in Table below. The cross section at the exit of the nozzle is 76.2 mm (width) ´ 76.2 mm (height), with an 1° expansion angle, and the total length is x = 710 mm measured to the diffuser. The test section of the SBR-50 facility is equipped with 2 pairs of quartz windows placed in the side walls of the duct for optical access and with 48 pressure ports along the top and bottom walls. It is equipped with M = 2 and 4 interchangeable nozzles. Important feature of this facility is the fast-response ohmic air heater allowing for operation at stagnation temperatures of T0 = 290-800K. The plenum is transformable to a heater configuration with a total plenum length of Lplenum = 4.5m and a total duct length of Ltot >7m (plenum, transitions, nozzle, test section, diffuser). The capacity of the vacuum tank is V=16m3 (right side in the image).
Instrumentation included:
- 64 channels static pressure system,
- set of fast pressure sensors (Kulite),
- fast camera imaging,
- high-definition time-resolved Schlieren system,
- Laser Differential Interferometry,
- Optical Emission Spectroscopic Analysis system,
- time-resolved PLIF and Mie scattering systems,
- CARS laser-OPO-based measurements system.
Table. Flow parameters, SBR-50.
SBR-50, Phase II | |
Mach number in test section: M | 0.2-1, 2, 4 |
Plenum pressure: P0, bar | 1-5 |
Stagnation temperature: T0, K | 290 – 800 |
Unit Reynolds number: Re, 1/m | 1-50·106 |
Air mass flow rate: ṁair, kg/s | up to 4.5 |
Duration of run, flow time / steady-state: t, s | 2 / 0.5 |
Time of readiness, period: T, min | 10 |
Hypersonic facility ND_ArcJet (ACT-1) – arc-heated M=6 wind tunnel with a circular free jet.
A key research facility located within the Hessert Laboratory at White Field is the arc-heated free-jet hypersonic test rig ND_ArcJet, former ACT-1. The ND_ArcJet is a pulsed-arc-heated hypersonic wind tunnel that is the only wind-tunnel at Notre Dame that is capable of simulating the high temperature conditions of hypersonic flight/reentry. The facility became operational in 2012 and offers a unique test platform for experimental studies of high enthalpy phenomena in hypersonic flows, non-equilibrium plasma-structure interactions, scramjet turbulent combustion problems, and materials’ testing.
The facility was deeply modifying in 2021 to increase the testing capabilities. A new design for the arc generation system has been developed that is based on standard stabilized-arc gas generator systems known as a “Huels-type” arc heater. This system utilizes tangential gas injection in conjunction with external magnetic coils to induce swirl in the flow that stabilizes the arc discharge and dramatically improves the durability and reliability of the arc-heating system. A second benefit of the Huels-type design is the ability to generate larger length arcs, resulting in much higher gas temperatures and operation at higher gas pressures. A schematic of the facility is shown in Figure below. Included in the figure is a rendering of the Huels-type arc heater and gas supply.

Schematics of the ND_ArcJet facility.
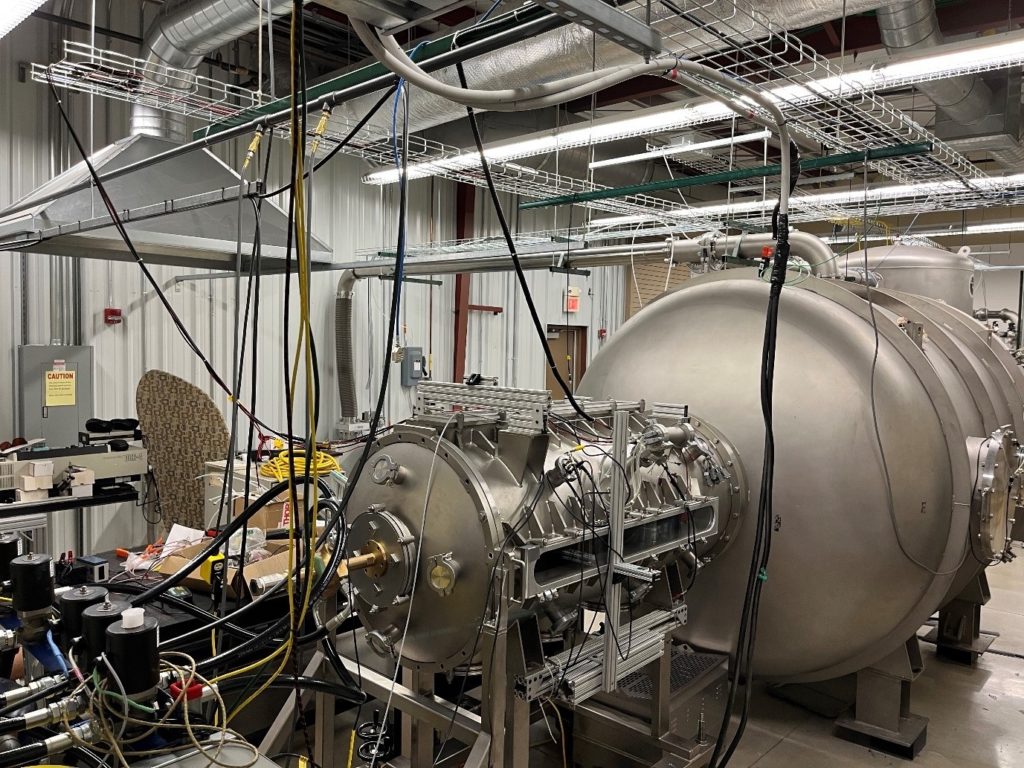
Photo of the test section/arc heater.
The flow parameters are as follows: flow Mach number M=4.5, 6 and 9; stagnation temperatures up to 6000K; total gas pressures up to 20bar; arc heating power up to 0.8 MW; high enthalpy flow run time up to 1s. The facility is equipped with high-speed imaging cameras, fast pressure sensors and Schlieren system. A significant drawback of the materials’ testing at the ND_ArcJet is a relatively short time of the hypersonic flow exposure. To overcome this, the test article is preheated by infra-red laser illumination of the surface up to a pre-defined surface temperature T=300-3000K.