Thousands of fans stormed to theaters over the first weekend of March 2024 to watch Denis Villaneuve’s highly anticipated Dune: Part 2. Incredible sci-fi visuals filled the big screen, including the fascinating Ornithopter, an aircraft that flies like a dragonfly. With so many modern aircraft inspired by biological flight, what makes insect-like flight, characterized by rapid flapping movements, difficult to engineer?
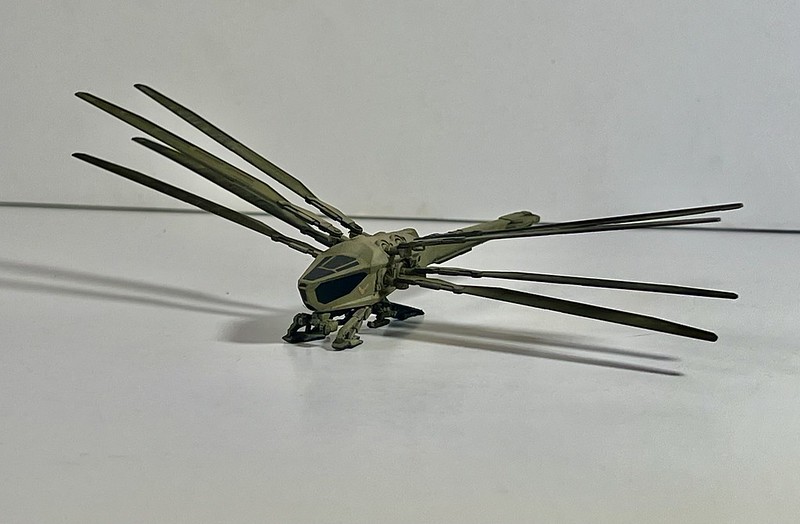
This question drove my fascination with insect wings and their unique biomechanical properties. They can perform complex aerial maneuvers, remain stable in turbulent environments, and sustain long flight times—all with tiny, delicate wings. We’ll dive into the mechanical and biological factors that make this possible and explore how understanding insect flight paves the way for possible engineering applications such as micro air vehicles (MAVs).
Continue reading “Dune’s Ornithopters: Future or Fantasy?”