Power to many is control, electricity, or strength depending on what one is talking about. But to muscles, it involves all three. When at the gym and thinking that someone looks powerful they usually have a lot of muscle. However, to control or activate all that muscle and use their strength it requires electrical power.
Continue reading “Power in Muscles”Tag: technology
Evolutionizing ALS Treatment: Can 3D-Printed Muscles Bring Hope to Patients?
ALS (Amyotrophic Lateral Sclerosis, a.k.a. Lou Gehrig’s disease) is is a rare but serious neurodegenerative condition that gradually causes muscle weakness and loss of control, eventually impacting the ability to move, speak, and breathe. It affects around 20,000-30,000 people in the U.S. at any time, with most cases diagnosed between ages 40 and 70.
Current ALS treatments are limited by a focus on symptom management and lack of understanding of the disease’s cause, but new technologies like 3D printing can offer exciting opportunities for innovation, such as custom prosthetics, artificial muscles, tissue engineering, and personalized medicine, which could significantly improve patient outcomes.
Continue ReadingCan Smartphone Overuse Permanently Damage Thumb Function?
Recently, a few studies(Inal et al. and Osailan) have been conducted on young people and adults regarding their pinch grip and hand grip strength. Shockingly those studies show that people who spend a long time using smartphones show very poor performance in their pinch and hand grip. We know our thumb is the finger used mostly for operating smartphones. It is also the most significant finger for any grip as well. Is it possible that the thumb is damaged permanently by overuse of a smartphone or is it just a correlation, not a causation?
Continue reading “Can Smartphone Overuse Permanently Damage Thumb Function?”Move Over Band-Aids, the Gecko is Here.
Band-Aids and stitches have been around forever. They are safe and common ways to address everything from paper cuts to deep wounds. However, these technologies each have their own drawbacks and researchers have looked to nature to improve upon them; enter the gecko, more specifically their feet. The goal of these scientists was to use the adhesive properties of a gecko’s foot pads as an alternative method to hold wounds closed, but how does this work?
What Makes Geckos so Clingy?
A gecko’s foot pads are unique instead of relying on any sticky substance, their toes have rows and rows of setae. Setae as you can see below are essentially rows of microscopic hooks that can cling in one direction. This causes no damage to the surface and because of the ways the setae are oriented, they are easy to remove from the surface in one direction. This is what allows a gecko to both cling to and easily remove their feet from a surface, or in our case makes adhesives made with this technique both secure and easier to remove than their counterparts.
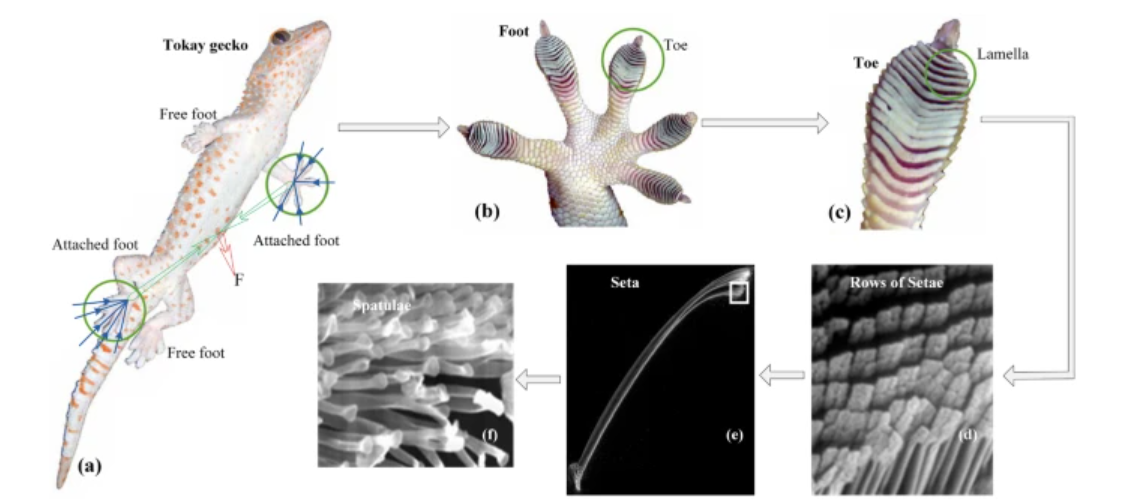
The Importance of Stickiness
Human skin is actually quite a rough surface that undergoes a lot of compression, tension and is further complicated by the existence of hair follicles and sweat. All of these factors make attaching anything like the gecko-based dry adhesive to the skin a daunting task. To get around this, bandaids rely on overpowering amounts of sticky substance and stitches are woven into the skin. This means that upon removal more damage and irritation to the wound can occurs. In a study the adhesive force of this technology was tested as well as the removal difficulty. It was found that this new method can achieve maximum closing forces slightly below that of sutures and is easier to remove than a bandaid of the same size. Notably, it does perform worse in wet or very humid conditions, so waterproof band-aids have a bright future.
The Design
A team of researchers published a study outlining the design, benefits, and drawbacks of a medical adhesive designed to mimic the gecko. This design encompasses the wound while providing a closing force to keep the wound closed. The amount of closing force imparted can be altered by changing both the number of legs and their thickness.
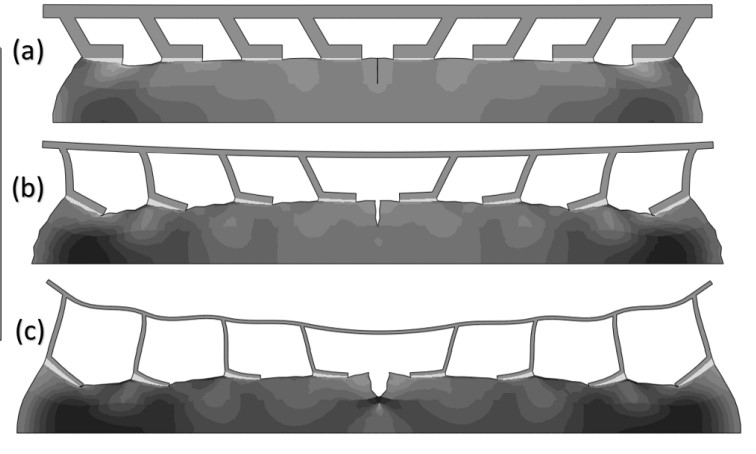
This is important because it means this method can be adapted to match the type of wound it is addressing. For a small cut a small adhesive with few legs can be used whereas, for a more serious wound, a larger adhesive layer with more, thicker legs will be used. This method also allows for air circulation allowing oxygen to reach to wound which promotes healing better than traditional methods. Using a gecko adhesive also minimizes wound irritation which can be a problem, especially for stitches and sutures which often cause irritation and even infection. Finally, this dry adhesive surface is biocompatible and can be made biodegradable. This means they will not react negatively with the skin and can safely dissolve in the body. This makes it a very desirable alternative to sutures which must be removed after insertion causing further wound irritation and requiring another visit to the doctor.
So while it may take a few years still don’t be surprised if you see dry adhesives for wound closings popping up on shelves; and when you see them know that they were inspired by the gecko. If you would like to learn more keep reading here.
Which is more stable, washing machines or birds? The answer might surprise you
What do birds and washing machines have in common? Shockingly, it’s not the ability to wash clothes. Rather, most birds and washing machines are great examples of vibration isolation systems.
Continue reading “Which is more stable, washing machines or birds? The answer might surprise you”Sticks and stones may break my bones but dirt will wash right off
There you are, sitting in the park eating your spaghetti picnic on your favorite picnic blanket when your pollen allergy acts up. You let out a sneeze powerful enough to compete with Aeolus’ bag of wind, but now your spaghetti is all over your favorite picnic blanket. You immediately go to rinse it off, but your fine Italian sauce has thoroughly soaked in. If only nature had a solution to keep a surface clean. Enter: the lotus leaf.
Continue reading “Sticks and stones may break my bones but dirt will wash right off”Using K-Motion Technology to Achieve the Perfect Baseball Swing
The question on every baseball player’s mind is: besides more practice, how can I improve my batting skills?
Continue reading “Using K-Motion Technology to Achieve the Perfect Baseball Swing”The Weight of Combat: Are powered exoskeletons the solution to heavy combat loads?
Have you ever wondered how much weight a soldier carries in a combat zone?
Continue reading “The Weight of Combat: Are powered exoskeletons the solution to heavy combat loads?”Skeletal Support Seekers’ Success (So Far)
Bones break, and broken bones need time to heal, or regrow. Fans of J.K. Rowling’s Harry Potter series are quite familiar with the concept of bone repair, as Harry is once required to drink a Skele-Gro potion to magically (and painfully) regrow his arm bones overnight. Now, as fantastic as it would be to completely fix broken bones in a few hours, modern medicine has not yet discovered that secret of the Wizarding World; however, several treatments have been developed in attempts to speed the rate of fracture repair as well as increase the comfort of the patient (take that, Skele-Gro).
Continue reading “Skeletal Support Seekers’ Success (So Far)”Robots Could Soon Replace Human Stunt-Doubles
Imagine an aerial acrobat soaring fifty feet above your head and executing gravity-defying stunts during a live performance. After your initial amazement that a human could be performing acts such as these so fearlessly, you look a bit closer to realize that the performer is actually not human at all. Thanks to a groundbreaking technology recently developed by Disney Research, this could soon become a reality.
Continue reading “Robots Could Soon Replace Human Stunt-Doubles”